Offshore wind developers must overcome myriad hurdles to complete a wind farm project. Perhaps one of the most challenging is navigating the ever-evolving global supply chain. To do this successfully, developers need powerful Market Intelligence.
Designed specifically for the offshore wind industry, Spinergie’s Supply Chain module delivers comprehensive data on components, manufacturing schedules, and transportation logistics—all in one intuitive platform. Whether you're sourcing suppliers, assessing manufacturing timelines, or planning vessel logistics, the module equips you with the insights needed to avoid the chaos of bottlenecks and find the opportunities that will see your project delivered on time and on budget.
This case study highlights how one offshore developer uses the solution to do just that.
Context
A wind farm developer with an international portfolio was in the research and development stage of a new mid-sized offshore wind farm in a mature region. Concerned about potential bottlenecks in offshore wind supply, they needed a tool to help them source the right components for their project and provide them with accurate data and analysis to help them successfully complete their project.
Challenge
To make their research more efficient, the team wanted to use a single-source planning tool as much as possible. They also wanted to use their Market Intelligence solution as a communication device where they could annotate, bookmark, and flag data points and intel. They also had to be able to access contextual data about the offshore wind market that would help them build the bigger picture in compiling their supply chain research.
Spinergie’s Market Intelligence Solution
Spinergie’s Market Intelligence solution combines the power of AIS-tracking data, updated every second, with in-depth analytics. The solution is modular, meaning clients can build the ideal solution to fit their needs with modules relevant to their operations. In this case, the client built a package relevant to offshore wind, including the supply chain module.
They primarily use the components database, manufacturing and transport schedules, and project fact pages for their supply chain research. Together, these elements help the team build a comprehensive picture of prior projects similar in scope to their upcoming development and better understand future market dynamics and where bottlenecks are most at risk of emerging.
Here are the Supply Chain features they predominantly use in their research:
The Components Database
The components database includes all the Tier 1 components of an offshore wind project (turbines, blades, towers, fixed and floating foundations, offshore substations, and array, export, and power cables) with over 130 specifications indexed.
Main features used:
Components Analysis: in the form of an interactive chart, the client can select multiple criteria to build their component analysis. Using the chart for each component, they can find out:
- How many components a manufacturer has supplied for projects in a region or for a specific wind farm project.
- The amount of installed capacity there has been for a specific turbine model.
- How many components a manufacturer has supplied per commissioning year.
- Competitive analysis - which developers have worked with which manufacturers.
Lead Times: For most Tier 1 components, lead times are increasing. By tracking lead times, the developer is better equipped to plan when they need to start manufacturer discussions to secure component supply and avoid delays. In the solution, each component has a lead time analysis chart showing two data sets:
1. Lead times between the preferred supplier agreement and installation start: this dataset helps the developer understand the timeline required between initial supplier discussions and project execution. Equipped with this knowledge, they can anticipate potential bottlenecks and align procurement strategies with project timelines.
2. Lead time between contract award and installation start: The client builds on the first point by assessing the efficiency of contract finalization processes. They can see how quickly previous projects have commenced after the contract award, which helps them create realistic timelines with their contractors.
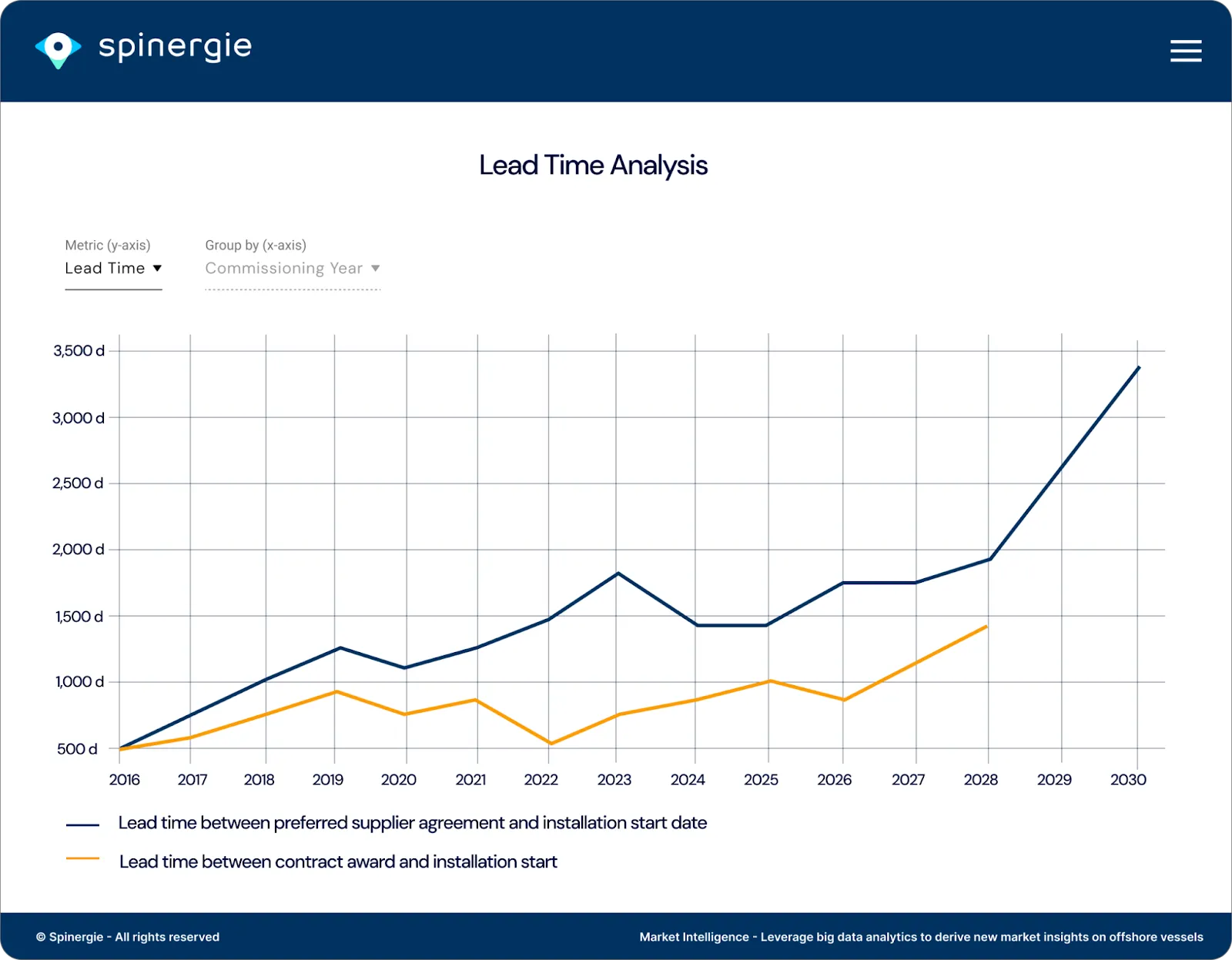
The Database: each Tier 1 component type (monopiles, jackets, towers, nacelles, etc.) has a database. This database can be customized to show relevant fields and remove less relevant fields. It can also be downloaded as an Excel sheet. The client uses this to build customized sheets they can share with the team.
- The client uses this database for several tasks: comparing technical specifications across multiple suppliers, evaluating potential suppliers based on their capabilities and experience, early identification of potential compatibility issues, and assessing which components will work best for long-term project viability.
Manufacturing Schedules
Manufacturing schedules contain the details of over 12,000 past and future manufacturing contracts. Each schedule follows Spinergie’s standard layout, with the option to select grouping metrics and timelines as needed. Events are highlighted, and each component has a tooltip with headline information and a click-through to the component page, which shows further granular analysis if required.
Manufacturing schedules help the client:
- Align their project schedule with manufacturer availability, making sure that timelines match up with their construction deadlines.
- Identify potential delays and potential alternatives should the need arise.
- Identify gaps or bottlenecks in the manufacturing pipeline and seek opportunities to secure early supplier agreements and gain a competitive edge.
- Make sure that their components will be available on time to meet any critical regulatory deadlines or funding milestones.
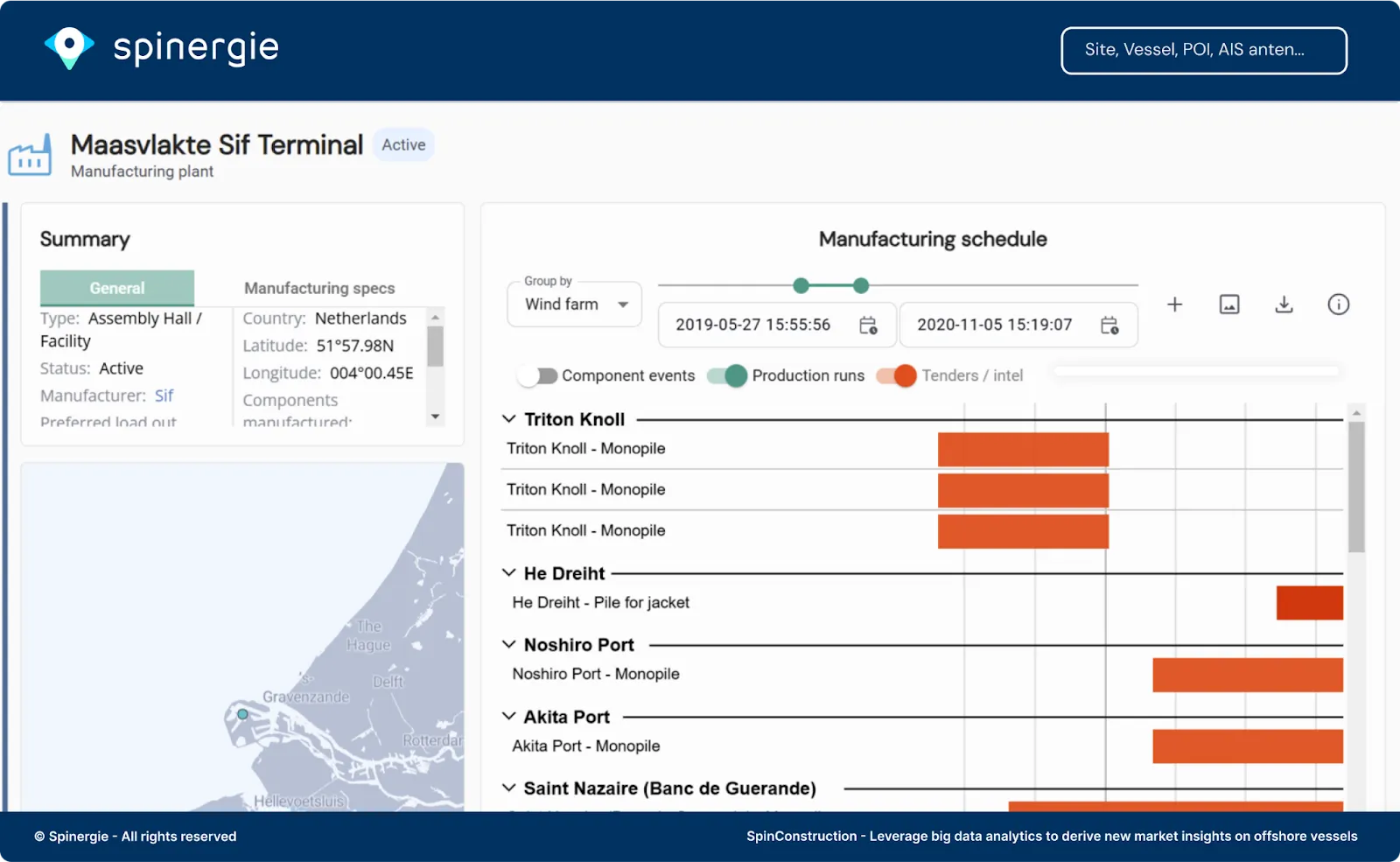
Project Fact Pages
Project Fact Pages are the ‘bibles’ of all offshore wind projects, showing all the granular details of their lifecycles. Each wind farm page has its own supply chain tab, with other tabs including project overview, installation, jackup and cable laying performance, operations performance, and location weather analysis.
The Supply Chain tab provides:
A Component Fact Sheet provides an ‘at a glance’ overview of the specs of each component used in the project. This is where the client can find quick answers to simple questions like what model was used, when the contract was awarded, and where the load-out location was.
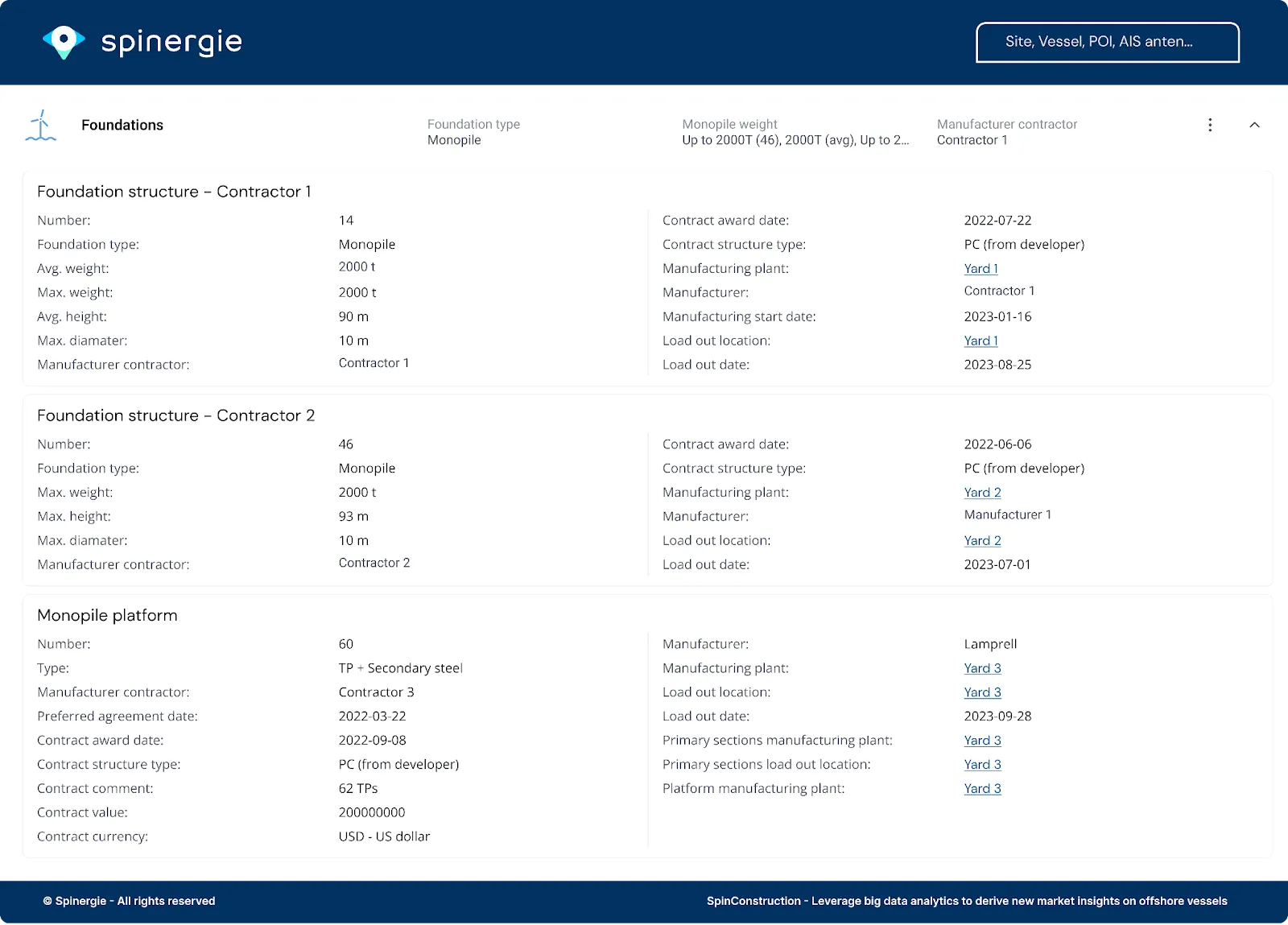
The Supply Chain Schedule is similar to the manufacturing schedule but specific to the wind farm project. It can be categorized using manufacturing criteria, component categories, or locations for multiple timeline analyses. Multiple date criteria include the start of manufacturing, the first and last load out, and the start of installation. The client can compare and contrast timelines to build a realistic picture of their timeline.
Manufacturing, contracts, and transport details is the ultimate database for the wind farm supply chain, providing extensive information on each element. Each component has a corresponding transport workpackage page, which gives vessel details, dates, and manufacturing data. This is where the client finds the details that will help them fine-tune their comparison analysis.
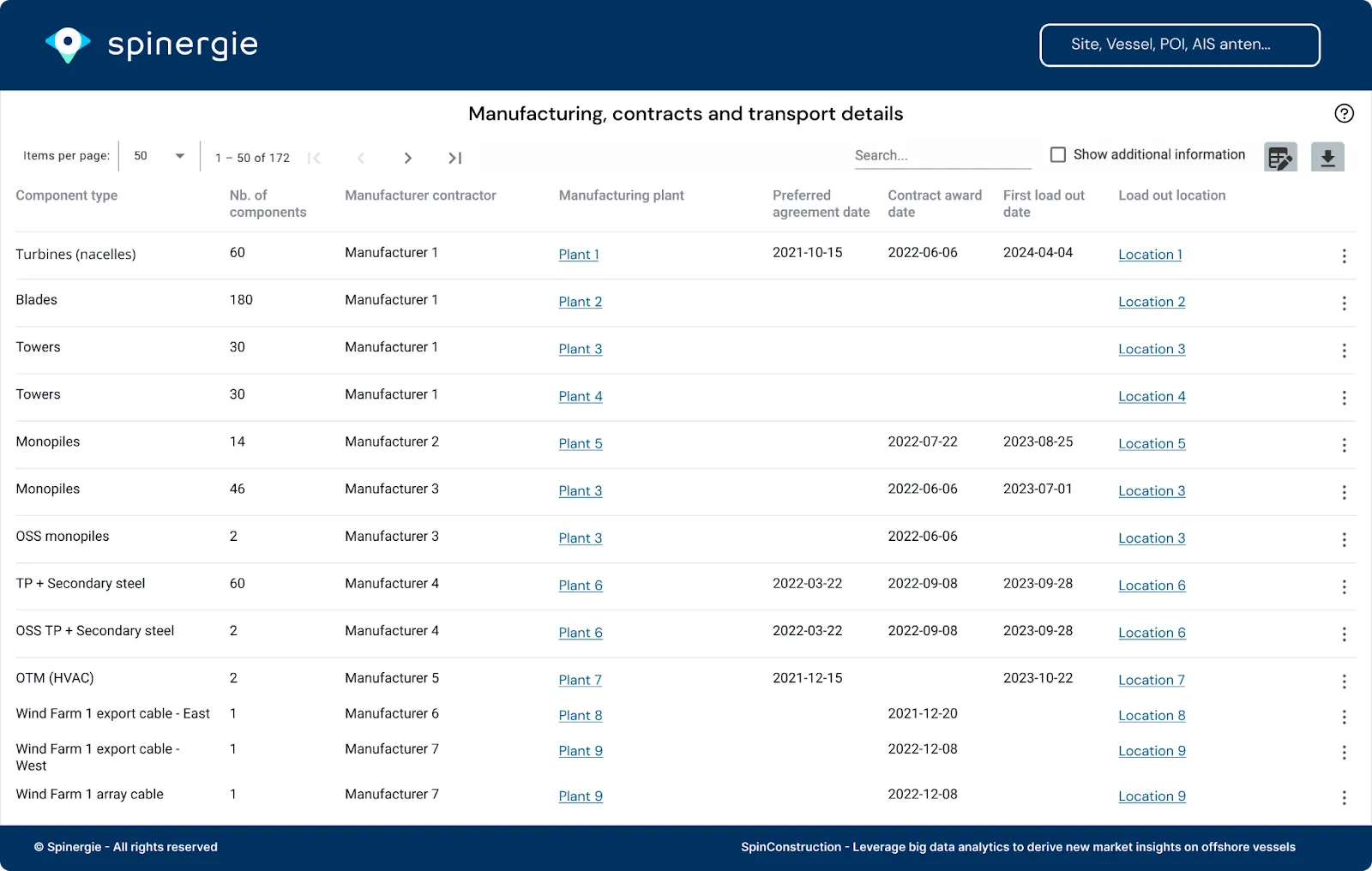
Component Transportation
Transportation is one of the client's main concerns, and vessel availability is expected to be one of the biggest bottlenecks as demand rises. The Component Transportation dashboard provides previous transportation analyses of commissioned or ongoing projects to help the client see what has worked and where and why there have been delays, helping them create mitigation strategies for their project.
The Component Transportation database utilizes AIS tracking data from more than 1,150 transportation vessels alongside publicly sourced intelligence to analyze trip details and durations. This analysis encompasses total durations, mobilizations, round trips, average loaded transit days, typical load-out times in port, the number of components transported (when available), and average times spent at delivery ports.
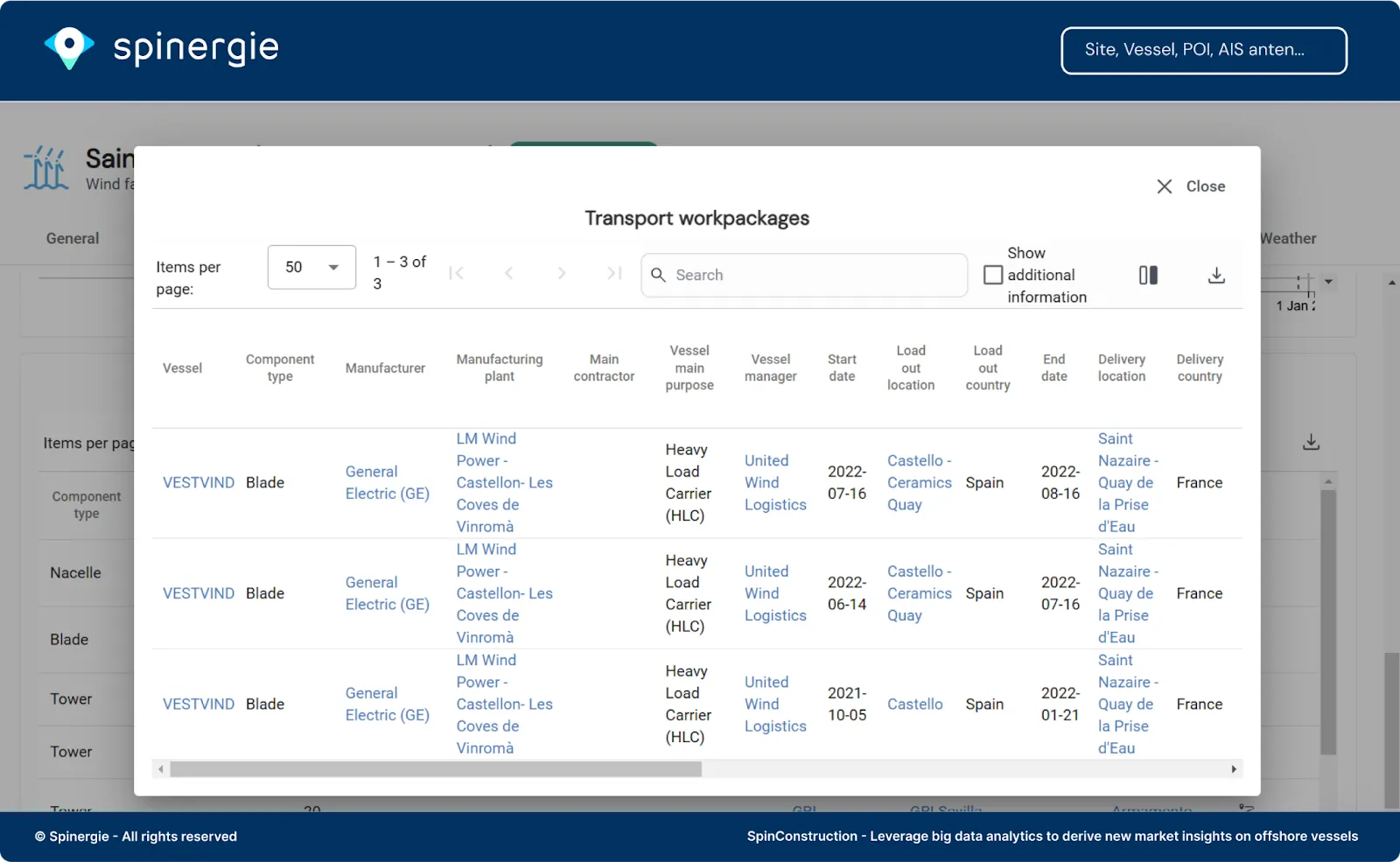
Read More in our White Paper: The Offshore Wind Supply Chain - Using close analysis of past performance to optimize planning processes
Result
Spinergie’s Supply Chain Module enhances our clients’ knowledge of offshore wind supply chain market dynamics and helps them strategically plan their projects. With instant access to component and manufacturing data and advanced analytics, the client has the tools to make informed sourcing decisions, secure suppliers efficiently, and avoid costly bottlenecks.
Main Benefits:
- A modular tool tailored to their intelligence requirements.
- Forewarning of potential bottlenecks.
- Insight into suppliers’ prior experience and performance to make decisions that match their needs.
- Access to probable transportation timelines to better negotiate realistic contracts with their suppliers.
- A single-source solution that acts as a communication hub for the team with features such as annotation and bookmarking.
Overall, Spinergie’s Supply Chain module helps the client save time by providing access to all supply chain details in a centralized source backed by selected additional modules for extra context. Furthermore, it reduces inefficiencies in the research process and ensures that critical insights are not overlooked.
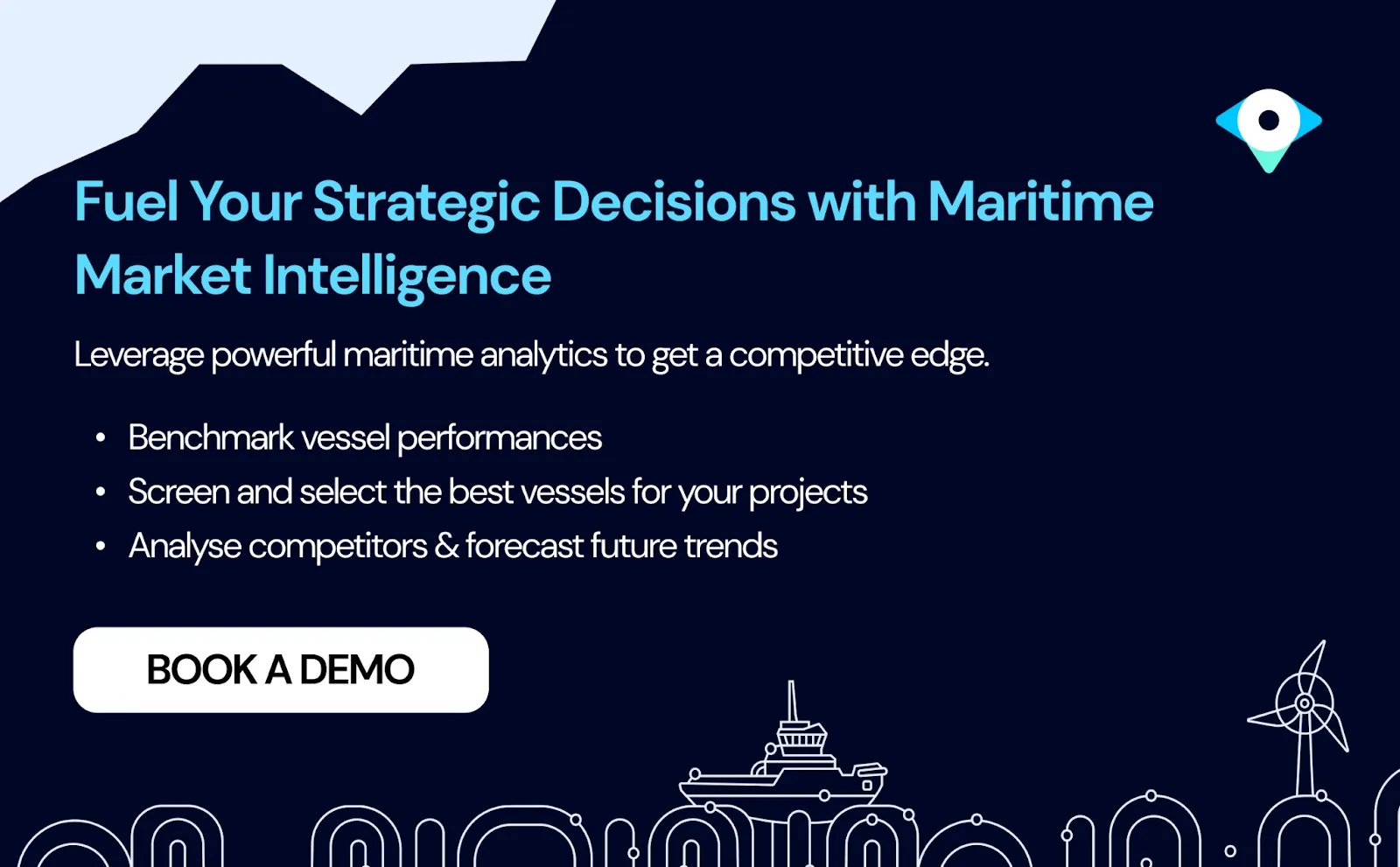