Offshore wind is booming with the latter half of this decade expected to see an exponential rise in the number of projects globally - including in emerging markets such as the USA. Spinergie analysis indicates that a total global capacity of 234 GW (across both fixed and floating projects) is forecast by the end of 2030 - a deadline many countries have imposed on themselves to meet ambitious offshore wind targets.
With this steep rise (the forecast for 2024 is just 43 GW in comparison), and significant growth outside of the maturing North Sea market, the industry can expect numerous supply chain challenges including the supply of power cables.
The rise in demand already putting pressure on the tightening cable market
The awarded length of offshore wind export cable grew from 759km in 2016 to almost 2,000km in 2022. Three main players: NKT, Nexans and Prysmian have shared more than 75% of that awarded length since 2016. The array cable market has also grown significantly with the yearly awarded length doubling in the last six years. Again, just three companies have the lion’s share of the market with JDR, Prysmian and Hellenic Cables taking 80% of the awarded length in that time period.
Lead times are also rising significantly. Since 2018, the duration between the award of an export cable contract and the start of the installation has almost doubled and is expected to keep growing in the coming years. There are just 10 significant cable manufacturers at present with four main companies sharing 85% of the market by awarded cable length. As observed in export cables, lead times are increasing significantly in offshore wind array cabling. The delivery date of cable awarded in early 2023 is mid-2025, totalling more than 800 days of lead time. EPCI contracts are seeing slightly longer lead times. A recent award from Tennet, for the delivery of nine subsea export cables for its 2 GW programme, is another good example of the increasing lead time, as it has a target of operating cables from 2029 to 2031.
Contracts need to be signed increasingly sooner to secure capacity. The distance from the shore is also increasing and export cables are getting longer, with the average length also doubling in six years. It is important to note that increased lead times are also being observed in power cables not dedicated to offshore wind, such as interconnectors. As electrification projects also gain traction and offshore wind weighs on the supply chain, cable manufacturing output is in high demand from both industries.
Boskalis and Subsea 7 top the vessel days charts for export and array respectively
While the manufacturing of cables is rising, it is also vital to assess the impact of increased demand on the installation campaigns themselves. In all, 17 contractors have been involved in wind farm export cable installation campaigns since 2016, however, over the last three years, just six companies shared 90% of the working time.
The top contractor by Cable Lay Vessel (CLV) vessel days is Boskalis which has been involved in many offshore grid projects in the North and Baltic Seas for Elia and TenneT. Prysmian is second in terms of vessel days with the manufacturer quick to enter new offshore wind cable markets such as France and now the USA at Vineyard Wind. Also notable is Subsea 7, which in the last three years has increased its presence in the export cables market, becoming the top contractor in terms of vessel days secured in 2022.
As for array cables, over the last three years, five companies totalled more than 90% of the CLV vessel days in such campaigns. Generally, the market share remains relatively stable, without any new players emerging. The busiest contractor is Subsea 7. From 2016 to 2022, the company totalled the most CLV vessel days in array cable campaigns and the most array cable sections installed. Subsea 7’s flagship cable-layer Seaway Aimery’s median performance (time spent to complete a section of cable between two turbines, including first-end and second-end pull-ins) is also the best within the period.
Distances increasing between factories and worksites, but plans are in place for more manufacturing sites
Since 2016, contracted CLV vessel days have grown by 22%, with growth accelerating in recent years due to an uptick in offshore wind activity. New demand is being absorbed by the delivery of new CLVs, such as Nexans’ Aurora and Leonardo Da Vinci, in addition to CLV specialising in actual cable-laying operations. However, the travelled distance of the CLV fleet is growing even faster than its contracted days, totalling 44% growth over the same period.
There are two aspects of the market which are causing this impact:
- Offshore wind is no longer unique to the North Sea. In recent years there has been significant cable demand from the Taiwanese offshore wind market which has seen accelerated growth in recent years. Additionally, a large proportion of Taiwanese projects opted out of using an offshore substation and instead chose to install large numbers of export cables. Projects in the USA have also begun adding mileage to the CLV fleet and will require many kilometres of subsea cables in the near future.
- Supply chain constraints are also hitting cable production. Manufacturers are feeling the pressure and taking the opportunity to build new cable plants in the USA (Nexans, Rise Light & Power, Prysmian), Europe (JDR, TKF, XLCC) and Taiwan (NKT). However, to face shorter-term delivery goals, production facilities are selected further and further away from the worksites. Examples include Seagreen 1’s export cables which were made in the USA, and Hollandse Kust Nord’s, which was manufactured in South Korea.
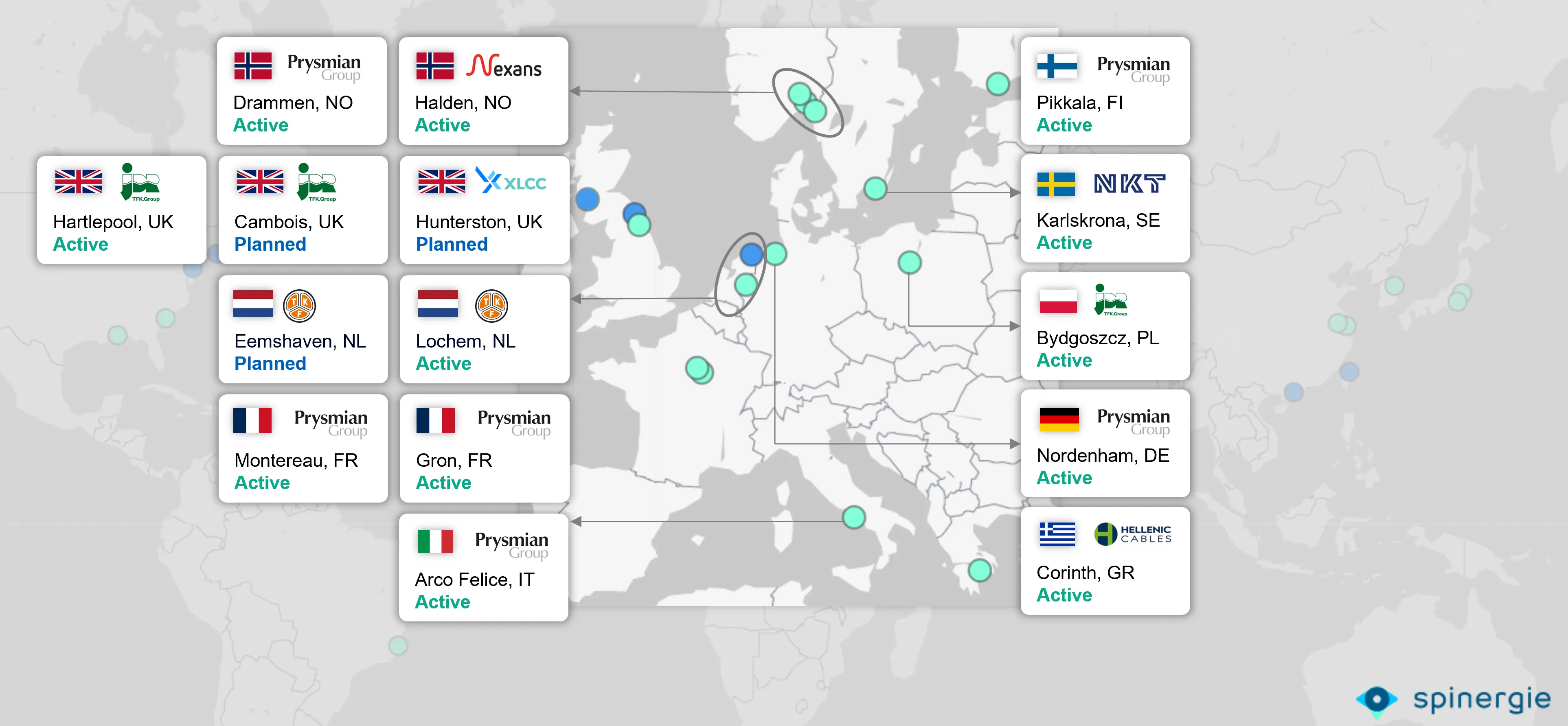
A number of new manufacturing sites are planned for in emerging countries such as the USA, Brazil and Taiwan with a number of new players also recently observed within the export cable market mainly from Asia. South Korea’s LS Cable has been involved in Taiwanese projects while a number of Chinese companies have been awarded European projects including Orient Cables for HKW VII and ZTT Submarine Cable for both Kaskasi and Gode Wind 3.
.webp)
Case Study: Vineyard
Due to the current lack of local infrastructure, however, and with a number of those new manufacturing sites only in the planning stages, developers have been resorting to sometimes convoluted options in order to complete cable installation projects in key regions such as the USA.
Vineyard Wind’s Vineyard 1 fixed offshore wind farm has been under construction since September 2022 with cable installation works ongoing. This part of the project has seen a considerable amount of mileage being undertaken by numerous vessels. It can be explained in three steps.
- Cable Enterprise (2001 built, Prysmian, CLV) crossed the Atlantic from Europe to the USA to lay the deepwater section of the export cable over the course of 27 days in Q4 2022.
- The cable was manufactured at Prysmian’s Pikkala Plant in Finland and then loaded onboard the Ulisse (2011 built, Prysmian, Barge). However, as Ulisse is a barge, in order to cross the Atlantic, the vessel had to be loaded onboard the Hua Yang Long (2012 built, Guangzhou Salvage, semi-submersible heavy load carrier) - which is understood to have taken approximately 27 days.
- Ulisse stays in the US after loading Cable Enterprise also to lay the shallow water cable section. As the cable was too long to be transported by Ulisse in one trip, a third cable layer, NDURANCE (2013 built, Boskalis CLV) was chartered just to transport cable from Pikkala in Finland to Ulisse in the US - a transit time of 31.9 days.
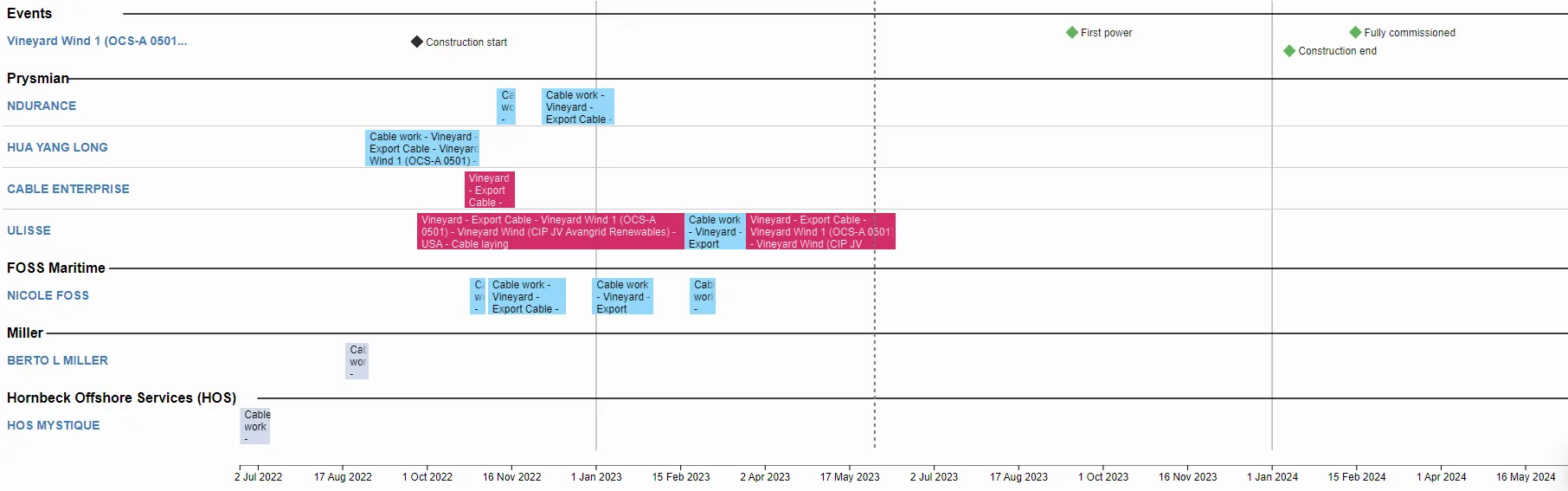
As the market continues to tighten and demand increases both for the cables and the vessels required in the installation campaigns these new manufacturing sites will only grow in importance. However, while plans are underway for these additional manufacturing sites in up-and-coming areas, bottlenecks are still a potential threat as time ticks towards those ambitious 2030 targets and many of the new sites are not likely to emerge before 2027.
Spinergie’s latest Market Intelligence module: Subsea Cables helps contractors and developers as they face up to increasing global supply chain challenges. They want to know what their market share is, which contractors they should select for a complex array scope and how to best execute a cable installation job with maximum efficiency. The Subsea Cables module gives clients the ability to answer these questions and more. Contact us for a demo for more information today.