Efficient installation is critical to the success of offshore wind projects with a direct impact on timelines, costs, and energy production goals. Yet, despite its importance, the industry often grapples with hardly predictable outcomes due to a complex interplay of technical, environmental, and operational factors.
For example, Spinergie analysis of U.S. installation programmes has shown dramatic variability with observations in a year-long period showing durations of between 1.1 days to nearly 50 days. Such a wide performance gap highlights the critical need to understand the factors driving these discrepancies.
Here we present six of the main drivers of installation performance from component or vessel type to regional discrepancies. This analysis has some key notes to keep in mind:
- It focuses on bottom-fixed turbines and foundations.
- Chinese and floating installations are excluded.
- Only ‘time at turbine’ is analyzed.
- Activities with a high level of duration uncertainty due to poor AIS coverage have been excluded.
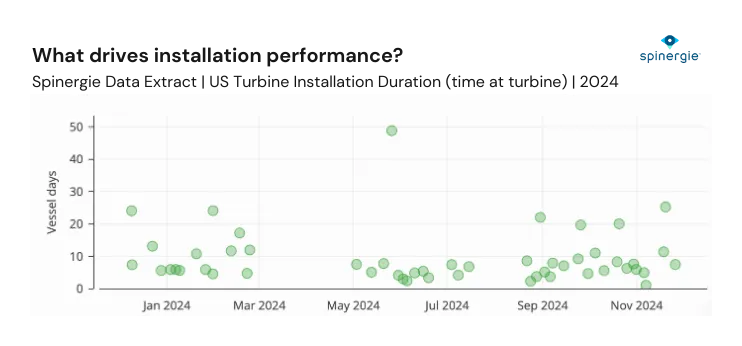
1. Jacket piling takes three times longer compared to monopiles
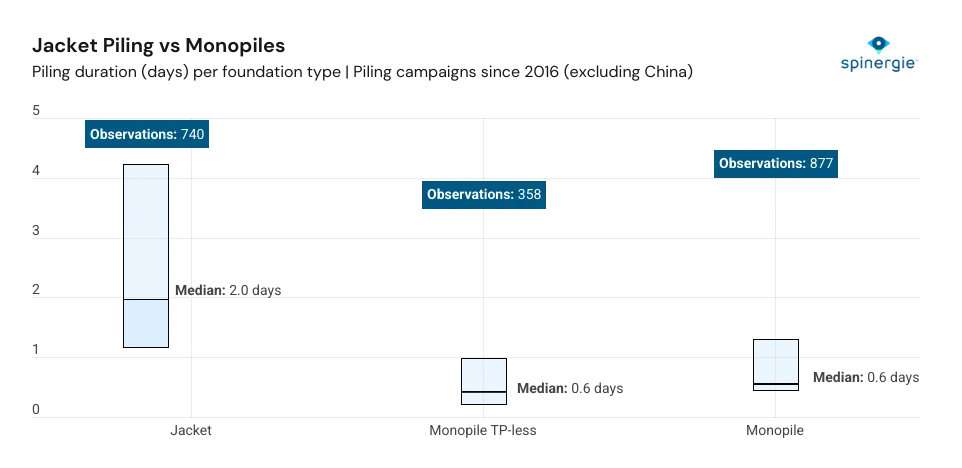
Installing piles for jacket foundations in offshore wind farms takes more than three times longer than for monopiles. This is because jacket foundations require multiple piles, usually three or four per foundation, and are generally installed at greater water depths. Furthermore, for jacket piling, the installation vessel is typically tasked with placing the piling template to ensure proper alignment, as well as removal afterwards, which adds additional time to the process.By comparison, installation times for traditional monopiles and TP-less monopile designs are similar. Both involve driving a single large pile into the seabed, with only minor differences in procedure.
2. Transition pieces (TP) and jackets take the same time to install
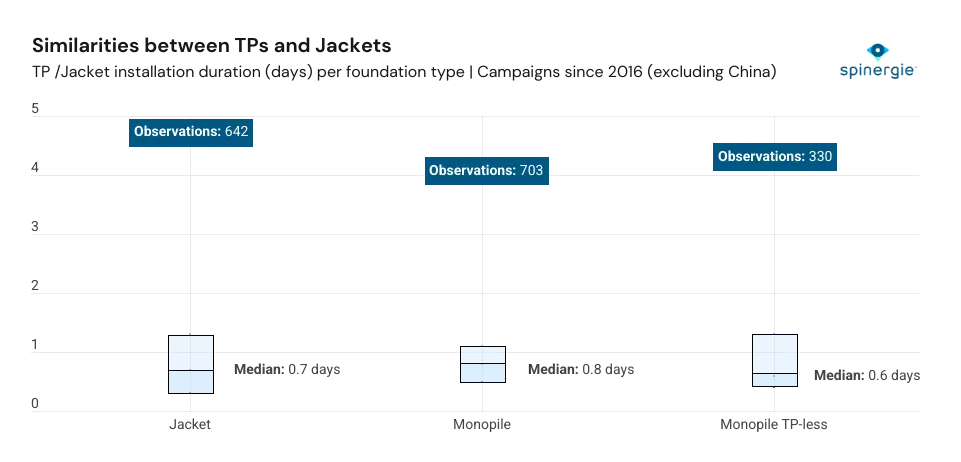
The installation of the upper part of the foundation, whether a jacket, transition piece, or secondary steel, typically shows similar efficiency across all foundation types, with a median installation time of less than one day.Monopiles, however, have the advantage of allowing the upper section to be installed by smaller vessels, such as Heavy Load Carriers, which is not feasible for jackets. Using smaller vessels reduces day rates, resulting in lower costs for the installer. HLCs such as Jumbo Maritime's Jumbo Javelin or Fairplayer are therefore increasingly used in offshore wind installations.
3. Vessel type has little impact on piling performance…
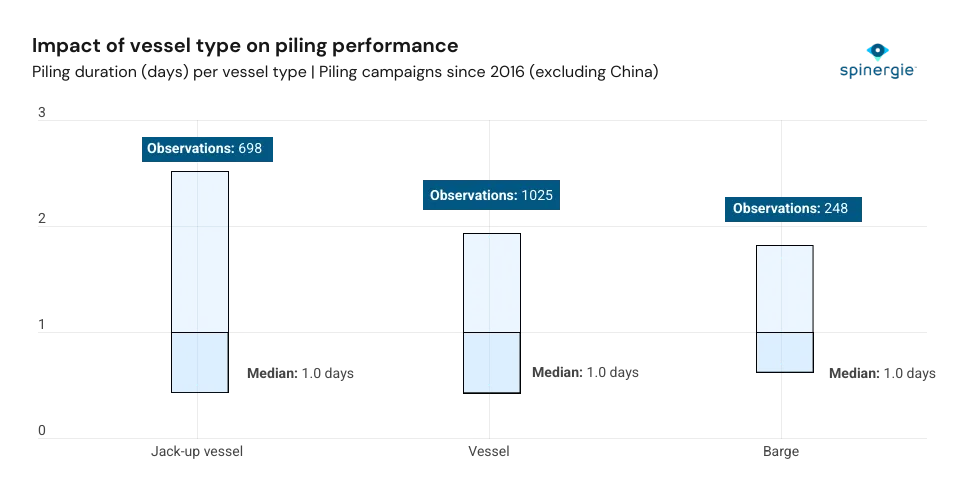
The installation method, using either a jack-up vessel with deployed legs or a dynamically positioned vessel or barge, has negligible impact on installation time. The median installation time for both monopiles and jackets remains approximately one day.Critical factors influencing piling time, such as operational efficiency, seabed conditions, and pile-driving equipment, play a larger role than the vessel type. Modern vessels and barges are equipped with similar tools and capabilities, resulting in comparable performance across platforms.
4.…and slightly impacts the TP and jacket installation
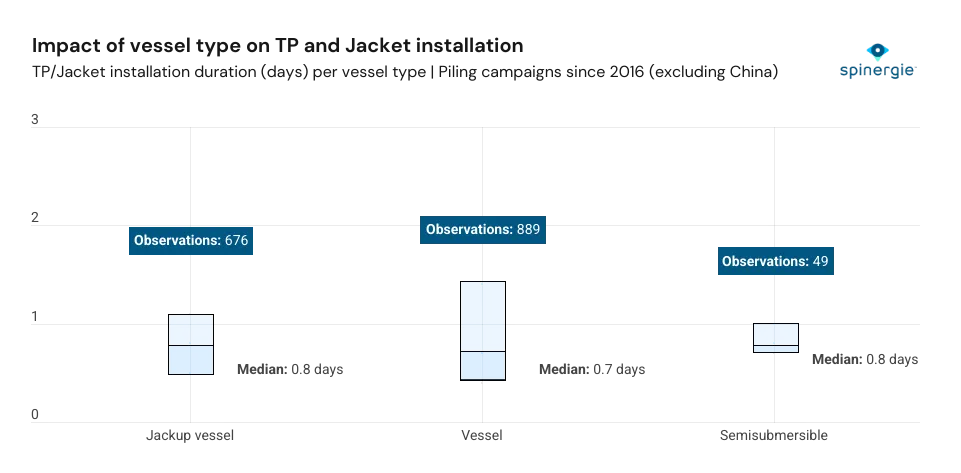
Jack-ups and vessels perform very similarly when it comes to installing the upper part of the foundations. However, jack-ups are more versatile and are also capable of installing turbines. This is one of the reasons why most vessel managers are ordering jack-up installation vessels.Semi-submersibles fit within their own special category here. Only around 50 installations have been observed since 2016, including the installation of jackets by the Saipem 7000 on EDF's Neart Na Gaoithe wind farm off the east coast of Scotland.
5. New-Gen turbines usually take longer to install
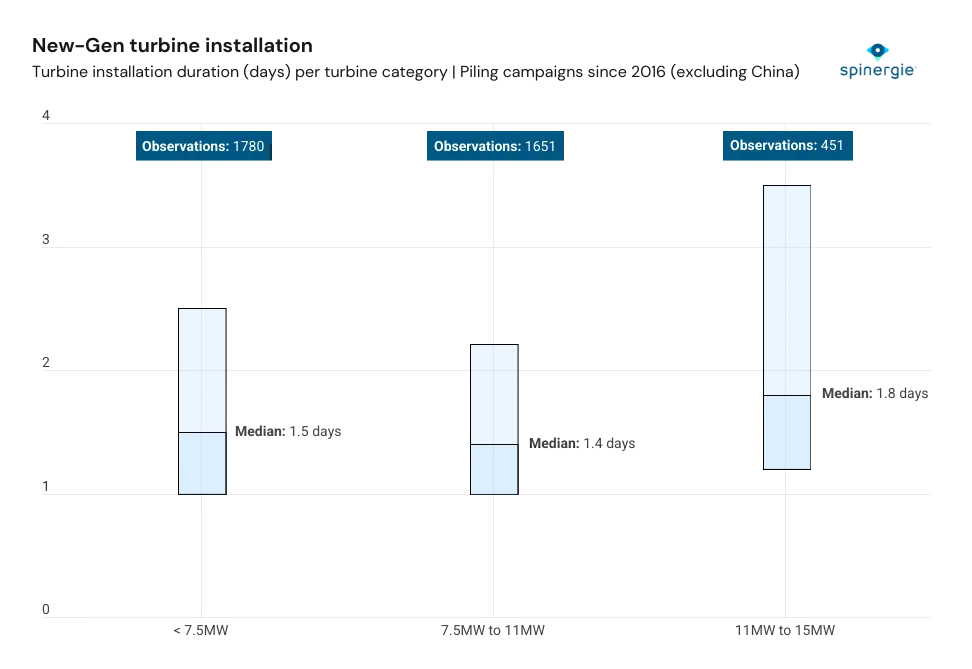
Installation durations of new-generation turbines, meaning those in the 11 to 15 MW range, are observed to be longer than smaller turbines. The significant value of the third quartile in this category, 3.5 days, underscores a high degree of variability for these installations. These performances are due to several specific factors:
- Larger turbines involve handling significantly larger components, such as towers, which are now frequently assembled in multiple sections. This requires additional lifts, increasing the complexity and duration of the process.
- Larger turbines are typically installed farther offshore, where harsher weather conditions and greater component heights create additional challenges. These factors reduce installation efficiency, as operations are more frequently interrupted by unfavorable weather and precise handling at greater altitudes is more difficult.
- Differences in turbine design and installation protocols among manufacturers contribute to variations in timelines.
As new-generation turbines become more prevalent, it remains to be seen whether installation times will converge with those of smaller turbines or whether these larger models will continue to demand longer durations.
6. Turbine installation times are five times longer in America than Northern Europe
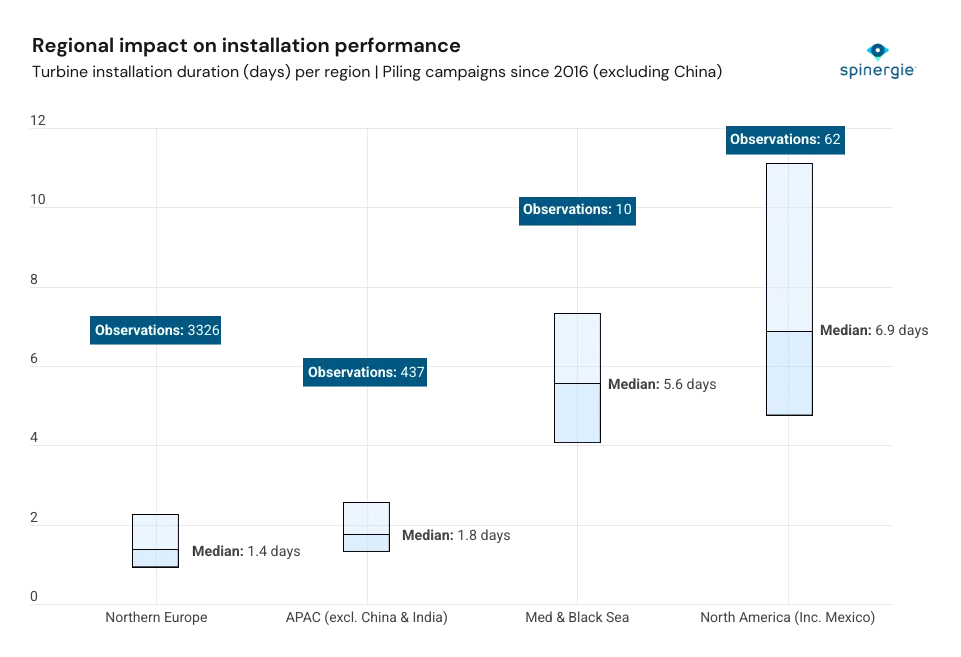
The pronounced regional differences in turbine installation performance are influenced by geographical factors, market dynamics, industry maturity, and weather conditions. These variations significantly affect installation timelines.
In North America, turbine installations take five times longer than in Northern Europe. Similarly, installations in the Mediterranean and Black Sea regions take about four times longer. These disparities are partly explained by the scale of activity: since 2016, (at the time of writing) only 62 turbine installations have been observed in North America and 10 in the Mediterranean Sea, compared to over 3,000 in the North Sea.
In the U.S., the Jones Act mandates the use of U.S.-flagged and built vessels for installation activities, necessitating other methods including feedering, installation from Canada or directly from the US without seabed preparation. This involves feeder barges transporting components to a Wind Turbine Installation Vessel (WTIV) for assembly, introducing additional logistical complexity and delays compared to direct installations. What's more, turbines installed in the U.S. are new-gen turbines, with an average size of 11.6 MW, compared with 6.2 MW in Northern Europe.
In contrast, installation performance in the Asia-Pacific (APAC) region is comparable to Northern Europe. The slight lag is attributed to less operational experience and the region’s exposure to more frequent and severe weather disruptions, which complicates scheduling and reduces efficiency.
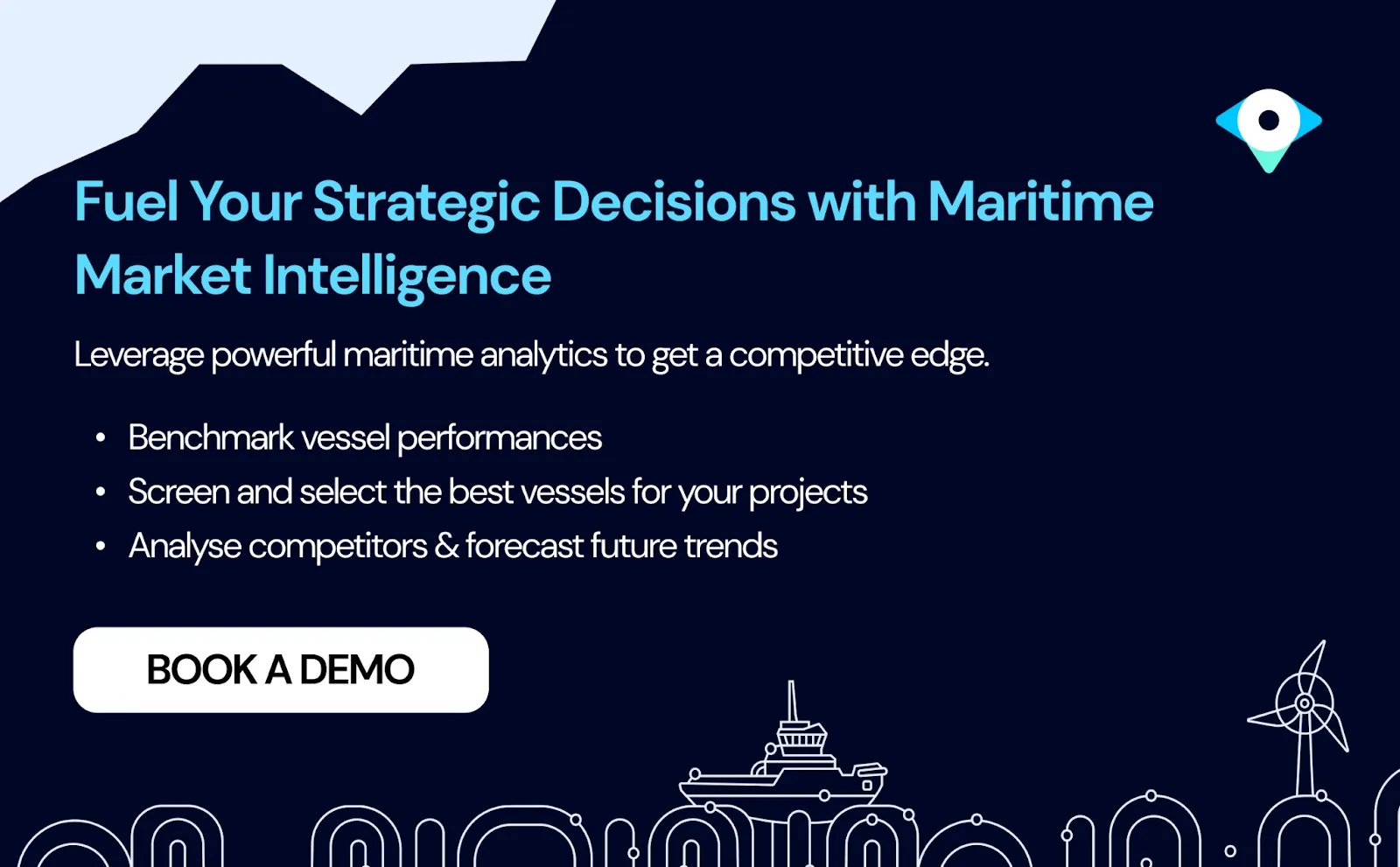